반도체 포토레지스트 중 Top coat material 은 생소한 소재중 하나에요.
왜냐하면 대부분이 Immersion ArF 쪽에서 사용되기 때문이죠
Top Coat material은 말그대로 맨 위쪽에 코팅하게되는 소재입니다.
그러면 이 소재는 무슨 역할을 하게 되느냐?
바로 물이 포토레지스트에 영향을 안주게 해주는게 주된 목적입니다.
왜 갑자기 물 이야기가 나오냐고 물으신다면~ Immersion ArF 자체가 물을 이용한 노광 방법이기 때문이에요~
193nm 침지 리소그래피는 3가지 종류로 나타납니다~
1. 용매 용해성 탑코트를 사용한 레지스트
2. 현상액 용해성 탑코트를 사용한 레지스트
3.탑코트 없이 레지스트의 세 가지 레지스트 공정 접근 방식을 가지고 있습니다.
현재 프로세스의 주류는 이들 중 두 번째인 종류입니다.
다만 추후 3번째로 탑코트 자체가 없는 방식으로 진화 예정입니다.
탑코트의 필수 요소는
첫째 레지스트 필름에 코팅되어 침출 및 수분 흡수를 방지하는 장벽층 역할을 합니다.
둘째 다음으로, 탑코트는 그 아래의 레지스트 필름과 물리적, 화학적으로 호환되어야 합니다.
셋째 마지막으로, 탑코트와 레지스트의 최상의 조합에 대한 공정 매개변수를 최적화해야 합니다.
여기부터는 전문적인 내용이라 맨 아래 사이트에서 참고한 내용을 나열할게요~
탑코트와 레지스트의 물리화학적 호환성
노출하는 동안 탑코트와 레지스트 스택이 물에 잠깁니다. 빛은 물과 탑코트의 계면뿐만 아니라 탑코트와 레지스트의 계면에서 반사될 수 있습니다. 탑코트의 굴절률(n외 투)는 물(n물) 및 저항(n반항하다)를 사용하여 파괴적으로 간섭하여 전체 반사를 줄입니다.
일반적인 193nm 레지스트는 1.7의 굴절률을 가지며 물은 1nm의 파장에서 44.193의 굴절률을 갖습니다. 식 (1)에 따르면, 침수를 위한 탑코트의 이상적인 굴절률은 ∼1.55이다.
Immersion lithography: topcoat and resist processes
Chemical compatibility is the key to success. Third in a series.
spie.org
탑 코트의 두께는 리소그래피 성능에 영향을 미치는 또 다른 중요한 매개 변수입니다. 이는 인터페이스의 반사가 파괴적으로 간섭하도록 최적화되어야 합니다. 입사각이 0인 조명의 경우, 즉 작은 개구수(NA) 상황에 해당하는 경우 탑코트 두께는 다음과
같아야 합니다.'
입사각이 높거나 NA가 높은 조명의 경우 시뮬레이션 도구를 사용하여 첫 번째 반사 최소값에 해당하는 최적의 두께를 계산해야 합니다. 광학 성능 외에도 두꺼운 탑코트는 침출 및 물 침투를 더 잘 방지합니다. 허용 가능한 침출 수준에 따라 목표 두께가 정의됩니다. 대부분의 현상액 용해성 탑코트에 권장되는 두께는 30-90nm 범위입니다.
탑 코트 용 용매는 레지스트와 반응하지 않아야합니다. 그렇지 않으면, 용매는 상도 코팅 공정에서 레지스트 표면을 부분적으로 용해시키고 혼합 층을 형성 할 수있다. 대부분의 193nm 레지스트는 프로필렌 글리콜 메틸 에테르 아세테이트(PGMEA)와 프로필렌 글리콜 모노메틸 에테르(PGME)를 용매로 사용하며 탑코트에는 알코올 기반 용매 시스템이 있습니다. 용매 비호환성은 레지스트와 탑코트가 다른 공급업체에서 공급될 때 발생할 수 있습니다. 새 탑코트를 배관하려면 라인의 솔벤트 세척 절차에 특별한 주의를 기울여야 합니다.
현상액 용해성 탑코트는 현상 모듈에서 수성 테트라메틸수산화암모늄(TMAH)에 의해 제거됩니다. 현상액의 높은 용출률은 탑코트의 효과적인 제거에 필수적입니다. 용해율이 높으면 '얼룩 결함' 수도 줄어듭니다. '위성 스폿 결함'이라고도 하는 블롭 결함은 주로 패턴 밀도가 낮은 영역에서 발견됩니다. 직경은 10-50μm입니다(그림 1 참조). 블롭 결함은 일반적으로 현상 및 헹굼 단계 동안 표면에 재증착된 탑코트 재료로 구성됩니다. 블롭 결함이 형성되는 메커니즘은 복잡하며 아직 조사 중입니다. 이는 현상액의 불균일성과 탈이온수 헹굼에 의한 급격한 pH 변화에 기인합니다. 대부분의 탑코트의 용해율은 100-1000nm/s 범위입니다.
두 번째 섹션의 세부 사항에서 설명했듯이 193i 노광 헤드의 물 메니스커스는 노광 중에 탑코트 표면을 가로질러 움직입니다. 후퇴하는 접촉각이 작을수록 물방울이 남을 가능성이 높아집니다. 후퇴하는 접촉각이 <>이면 수막이 남게 되는데, 이를 '필름 풀링'이라고 합니다.1 남겨진 물은 원형 워터 마크를 형성합니다. 이를 줄이거나 제거하려면 큰 후퇴 접촉각이 필요합니다. 이것은 탑코트 표면의 소수성을 증가시킴으로써 실현될 수 있다. 그러나 이 요구 사항은 Blob 결함을 줄여야 하는 요구 사항과 모순되는 것 같습니다. 소수성 탑코트는 현상액에서 낮은 용해율을 갖는 경향이 있는 것으로 관찰되었다. 여기에서 신중한 최적화를 구현해야 합니다. 형성 메커니즘과 자세한 환원 전략은 이 시리즈의 이후 기사에서 논의될 것입니다.
용매 용해성 탑코트 접근법은 노광 후 수성 TMAH 현상액이 아닌 용매에 의해 제거된다는 장점이 있습니다. 수성 TMAH 현상액에서의 용해 속도를 고려하지 않고, 용매 가용성 탑코트는 매우 소수성으로 설계될 수 있다. 물 후퇴 접촉각은 100° 이상일 수 있습니다. 용매 용해성 탑코트를 사용하면 침지 결함 수를 줄일 수 있음이 입증되었습니다2 0.1/cm까지2.
탑코트 및 레지스트 조합의 암석 평가
지금까지 모든 193nm 레지스트와 잘 작동할 수 있는 범용 탑코트는 없지만 탑코트 공급업체에게는 매우 매력적인 목표입니다. 다양한 현상액 용해성 탑코트가 시장에 나와 있으며 탑코트와 레지스트의 다양한 조합이 테스트 및 평가되었습니다.3 전체 리소그래피 성능을 비교하면 성능이 우수한 레지스트/탑코트 스택을 식별할 수 있습니다.
그림 2 (a)는 선폭이 90nm이고 공간 폭이 90nm 인 고밀도 형상의 하향식 이미지를 보여줍니다 (이하 90nm / 90nm로 설명), 다른 탑 코트 (TC1, TC2 및 TC3)로 Resist A에서 제작되었습니다. 이미지는 최상의 선량과 초점으로 촬영되었습니다. 쉽게 비교할 수 있도록 모든 사진의 크기는 1μm x 1μm로 동일합니다. 레지스트 A와 TC2의 조합에서 레지스트 라인이 끊어지고 왜곡되는 매우 호환되지 않는 상황이 관찰되었습니다. TC3이 있는 레지스트 라인의 LER(1σ)은 ∼8.7nm이고 TC3이 있는 경우 ∼8.0nm입니다. 이러한 결과는 탑코트가 LER에 어느 정도 영향을 미친다는 것을 나타냅니다. 공정 창은 그림 2(b)에 90nm의 임계 치수(CD) 목표와 ±10%의 허용 오차를 가지고 표시됩니다. TC2에서는 공정 윈도우를 얻을 수 없으며 TC1에서는 가장 큰 공정 윈도우를 얻을 수 있습니다. 단면은 레지스트 라인의 프로파일과 레지스트 필름 손실의 심각성에 대한 훨씬 더 나은 통찰력을 제공합니다. 최상의 선량과 초점(하향식 이미지에 해당)에서 레지스트와 탑코트 조합의 단면 이미지도 그림 2(a)에 나와 있습니다. 호환되지 않는 조합인 레지스트 A/TC2는 레지스트 패턴의 높이가 공칭 레지스트 두께의 40% 미만인 상당한 레지스트 손실을 나타냅니다. 상반올림은 TC1 및 TC3 모두에서 관찰되었으며, 이는 상도복이 레지스트 손실을 유발할 수 있음을 시사합니다.
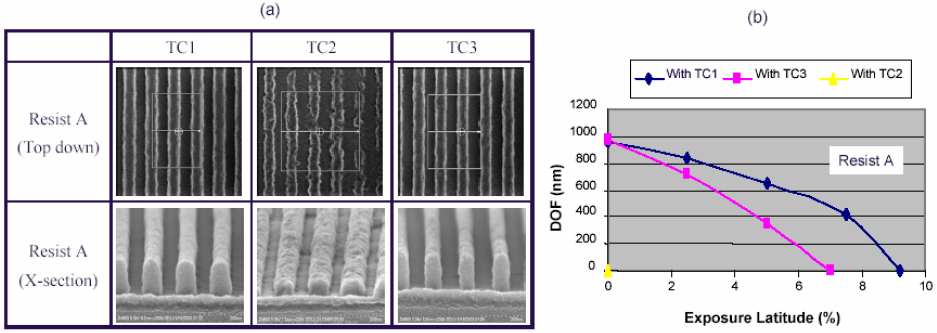
레지스트 필름 손실을 추가로 조사하기 위해 레지스트 A/TC1, TC3 및 TC4의 스택에서 대비 곡선을 측정했습니다(레지스트 A 및 TC2와의 호환성이 좋지 않아 TC4를 건너뛰었습니다). 노광 전 레지스트 필름의 두께는 200nm입니다. 그림 3(a)는 측정된 대비 곡선을 보여줍니다. 선량이 E0로 증가하면 TC4가 있는 레지스트가 가장 많은 두께를 잃습니다. (E0는 레지스트 필름을 완전히 노출시키는 데 필요한 최소 선량 값입니다.) TC1은 저항 손실을 최소화합니다. 그림 3 (a)는 또한 1 개의 탑 코트 모두에서 레지스트 다크 손실 (즉, 노광없이 탑 코트를 제거한 후 레지스트 두께의 변화)이 무시할 수 있음을 보여줍니다. 이는 탑코트-유도 레지스트 손실이 광반응에 의한 것일 수 있음을 시사한다. 레지스트 A와 TC3, TC4 및 TC90의 스택은 90nm/3nm 조밀한 패턴에 대해 동일한 선량과 초점으로 노출되었습니다. 단면 이미지는 다른 탑코트가 있는 레지스트 패턴에서 촬영되었습니다(그림 50(b) 참조). 레지스트 A/TC4 스택에서 약 1nm의 레지스트 손실이 측정되는 반면, TC30의 경우 레지스트 손실은 약 1nm에 불과합니다. 앞에서 설명한 전체 리소그래피 성능(프로세스 윈도우, LER, 프로파일, 레지스트 손실 등)을 비교함으로써 레지스트 A/TC<> 스택이 테스트된 변형 중에서 최적의 조합으로 식별됩니다.

프로세스 최적화
레지스트/탑코트 스택은 세 가지 베이킹 단계를 거쳐야 합니다: 레지스트의 적용 후 베이크(PAB); 탑 코트의 PAB; 및 노출 후 베이크(PEB). 세 가지 베이킹 단계에는 특정 효과가 있습니다. 레지스트와 탑 코트의 PAB는 대부분의 용매를 제거합니다. 레지스트 용매의 증발은 또한 레지스트에서의 광산 발생제(PAG) 분포에 영향을 미친다. PEB는 탈보호, 광산의 확산 및 현상액에서 탑코트의 용해율에 영향을 미칩니다. 최상의 성능을 얻으려면 베이킹 온도를 최적화해야 합니다.
실험 설계('실험 설계' 또는 DOE라고 함)는 Resist A/TC1 스택으로 수행되었습니다. 다른 모든 파라미터는 동일하게 유지되었고, 단지 베이킹 온도만 변경되었다. DOE 매트릭스에는 공급업체에서 권장하는 온도 외에도 레지스트 PAB 및 PEB 온도의 위와 아래 5°C와 탑코트 PAB 온도의 위와 아래 10°C가 포함됩니다. 대비 곡선은 상이한 베이킹 온도에서 측정되었다. 그림 4 (a)는 결과를 보여줍니다. 대비 곡선에 대한 온도의 강한 영향이 관찰되며, 특히 어깨 영역에서 관찰됩니다. 숄더 영역에서 105°C/80°C/110°C(레지스트의 PAB 온도/탑코트의 PAB 온도/PEB 온도)의 온도 조합은 레지스트 손실을 최소화합니다. 그림 4(b)는 105°C/80°C/110°C의 온도와 공급업체 권장 온도(기록 또는 POR의 프로세스는 110°C/90°C/115°C)에서 베이킹된 레지스트 패턴의 단면 이미지를 보여줍니다. 노출 조건(조명 설정, NA, 마스크, 선량 및 초점)은 단면 웨이퍼에 대해 동일합니다. 분명히 POR 베이킹 온도로 처리된 레지스트 패턴은 10°C/105°C/80°C에 비해 ∼110nm의 추가 레지스트 손실이 있습니다.

레지스트와 탑코트의 최적화된 PAB 온도는 POR의 온도보다 낮으며 PEB 온도를 변경할 필요가 없습니다. PAB 온도를 낮추는 것은 레지스트의 PAG 분포와 관련이 있습니다. 레지스트 PAB 단계에서 열 에너지는 레지스트 용매를 증발하는 표면으로 구동합니다. 레지스트의 벌크에서 PAG의 일부는 또한 용매 흐름에 의해 레지스트 표면으로 끌려간다. 탑코트 PAB 단계에서, 레지스트 용매 증발 및 레지스트 표면으로의 PAG 이동은 탑코트 PAB도 레지스트를 베이킹하기 때문에 다시 일어난다. POR 레지스트 PAB 온도는 공급업체에서 권장했습니다. 193nm '건식' 리소그래피 공정에 최적화되어 있으며, 하단 반사 방지 코팅에 단층 레지스트를 사용합니다. 그러나, 침지 공정에서, 레지스트 PAB 온도는 탑코트 베이크를 수용하기 위해 감소되어야 한다. POR 온도에서 레지스트는 실제로 탑코트 PAB에 의해 오버베이크되고 더 많은 PAG가 레지스트 및 탑코트 인터페이스로 이동됩니다. 높은 PAG 농도는 우리가 관찰한 바와 같이 노출 및 발달 후 추가 저항 손실을 유발합니다. 원칙적으로, 레지스트 PAB 온도는 탑코트의 PAB가 생략될 수 있는 경우 '건식' 리소 공정과 동일할 수 있습니다. 그러나, 이는 소성 온도의 감소에 따라 탑코트의 배리어 성능이 저하되기 때문에 바람직하지 않다.
193I 상도장 없이 공정 저항
상부 보호 코팅이 없는 레지스트 공정은 193 침지 리소그래피를 대량 생산에 도입하는 데 선호되는 솔루션입니다. 이러한 단순화된 공정은 탑코트 재료에 대한 별도의 코팅 및 베이킹 단계 없이 진행되므로 소유 비용이 절감되고 결함 원인이 줄어듭니다. 그러나 문제는 물에서 최소한의 침출과 우수한 전체 리소그래피 성능을 동시에 제공하는 것입니다. 혁신적인 레지스트는 이 접근 방식의 성공을 보장하는 열쇠입니다. 레지스트 공급업체는 이 목표를 적극적으로 추구하고 있습니다.
다양한 193i 전용 레지스트가 평가되고 탑코트 공정과 비교되었습니다.4 바이너리 마스크로 얻은 90nm 조밀 특징의 공정 창은 그림 5에 표시되어 있습니다. 90nm의 line-CD 타겟과 ±10%의 CD 허용 오차에서 최대 DOF는 1.0μm이고 최대 노출 관용도는 8%입니다. 기준 공정의 공정 창도 비교를 위해 그림 5에 표시되어 있습니다. 이 기본 공정은 건식 레지스트와 현상액 용해성 탑코트의 다양한 조합 중에서 선택되었으며 여전히 우수한 성능을 보여줍니다. 기준 공정과 비교하여 탑코트가 없는 현재 193i 레지스트의 공정 창은 약 15-20% 더 작으며, 이는 레지스트 공급업체가 물과 직접 접촉할 때 높은 리소그래피 성능과 낮은 침출 거동의 요구 사항을 동시에 충족하는 레지스트 구성 요소를 선택하는 딜레마를 나타냅니다.

탑코트가 없으면 아민 오염은 화학 증폭 레지스트의 문제입니다. PEB 지연은 레지스트 라인 CD 변화 대 PEB 지연 시간을 테스트하기 위해 평가되었습니다. 웨이퍼는 고정된 선량과 초점으로 노출되었습니다. 노출 후 웨이퍼를 1분, 3분 및 10분 지연 시간 동안 트랙에 저장했습니다. 이 지연 후 웨이퍼는 PEB 및 개발로 보내졌습니다. 90nm/90nm 레지스트 패턴의 CD는 웨이퍼 전체에서 측정되었습니다: 레지스트 프로파일 변화를 더 잘 모니터링하기 위해 레지스트 라인의 상단과 하단 모두. 측정된 CD는 웨이퍼 전체에 걸쳐 평균을 냈고, PEB 지연 시간의 함수로서 그림 6에 표시되었다.

그림 6의 상단 및 하단 CD는 PEB 지연 시간이 10분으로 변경되지 않았습니다. 이는 레지스트 프로파일이 트랙 내부에서 최대 10분 동안 PEB 지연에 대해 동일하게 유지됨을 의미합니다. 우리는 또한 다른 PEB 지연 시간으로 웨이퍼의 단면을 만들었습니다. 레지스트 패턴의 프로파일은 최대 10분의 PEB 지연으로 변하지 않으며, 이는 레지스트 공정이 PEB 지연에 대해 매우 견고함을 나타냅니다. 가능한 설명은 트랙과 스캐너가 연결되어 있고 Lithius 트랙 내부의 아민 레벨이 ∼0.5ppb라는 것입니다.
탑코트가 없는 레지스트 공정은 잠재력이 있고 193i 리소그래피에 선호되는 솔루션이지만 현재 샘플의 성능은 여전히 탑코트 공정보다 뒤쳐져 있습니다. 현상액 용해성 탑코트가 현재 주류이지만 레지스트와의 호환성 문제에 주의를 기울여야 합니다.
침지 리소그래피: 탑코트 및 레지스트 공정 (spie.org)
Immersion lithography: topcoat and resist processes
Chemical compatibility is the key to success. Third in a series.
spie.org
여러가지로 반도체의 소재쪽 세상은 넓고 다양한것 같습니다~
차근차근 공부해서 전문가가 되어 보아요~
'반도체 기초' 카테고리의 다른 글
포토레지스트 소재 TARC & BARC (2) | 2023.02.28 |
---|---|
스페이서 이중패터닝 기술 spacer patterning technology (SPT) (1) | 2023.02.21 |
Spin on hardmask (SOH) (SOC) (1) | 2023.02.21 |
Fine metal mask (FMM) (1) | 2023.02.21 |
포토레지스트 Positive Negative 타입 비교 (1) | 2023.02.15 |